We have accumulated over two decades of technical expertise in fluoropolymer coating and lining, leading to the development of proprietary sintering methods tailored for highly corrosive and demanding environments. To address persistent challenges in industrial processing, such as corrosion, abrasion, and high-temperature vacuum stability, we've introduced three innovative sintering techniques reinforced with steel mesh layers.
Performance Comparison of Fluoropolymer Sintering Methods Listed in order of overall performance from left to right.
High purity liquid fluoropolymer coating sintering process (thin/thick layer mesh reinforced) (new process) | Ultra-pure powder fluoropolymer coating sintering process (thin/thick layer mesh reinforced) (new process) | Common filling materials sintering process (thin/thick layer mesh reinforced) (new process) | Standard high purity liquid fluoropolymer sintering process | Standard ultra-pure powder fluoropolymer coating sintering process | Common powder filling materials sintering process | |
Service life | 15–20 years (based on actual usage) | 10–15 years (based on actual usage) | 3–5 years (based on actual usage) | 1–3 years (based on actual usage) | 1–3 years (based on actual usage) | 0.5–3 years (based on actual usage) |
Spark test (pinhole resistance) | 1.8–2.2 mm,withstands up to 30,000V | 1.8–2.2 mm,withstands up to 25,000V | 1.8–2.2 mm,withstands up to 20,000V | 0.8–1.2 mm,withstands up to 15,000V | 0.8–1.2 mm,withstands up to 16,000V | 0.8–1.2 mm,withstands up to 16,000V |
High-temperature vacuum resistance | ≥240°C,stable under extreme vacuum | ≥240°C,stable under extreme vacuum | ≥220°C,stable under extreme vacuum | ≥150°C,stable under extreme vacuum | ≥150°C,stable under extreme vacuum | ≥150°C,stable under extreme vacuum |
Cross-section Structure (from Top to Bottom)
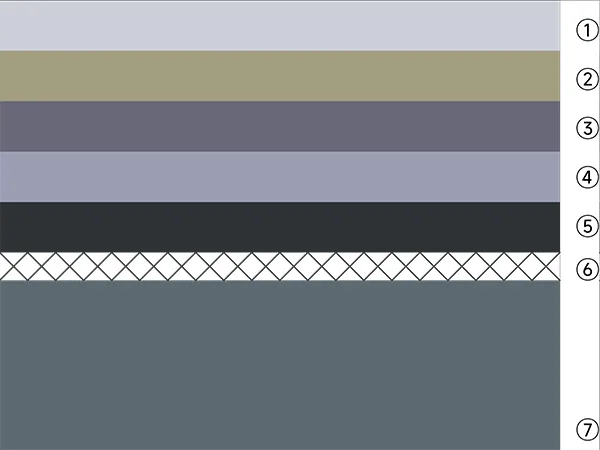
- 1. Topcoat
- 2. 0.8-1mm intermediate coat
- 3. 0.3mm intermediate adsorption layer (to prevent acid liquid and acid gas from penetrating)
- 4. 0.8-1mm intermediate coat
- 5. 0.2mm primer
- 6. Steel mesh
- 7. Metal panel
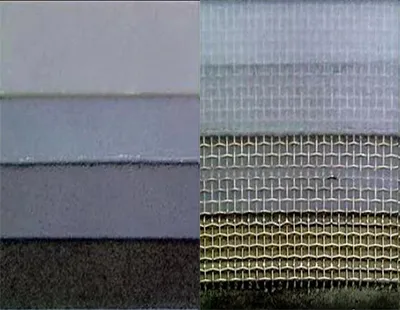
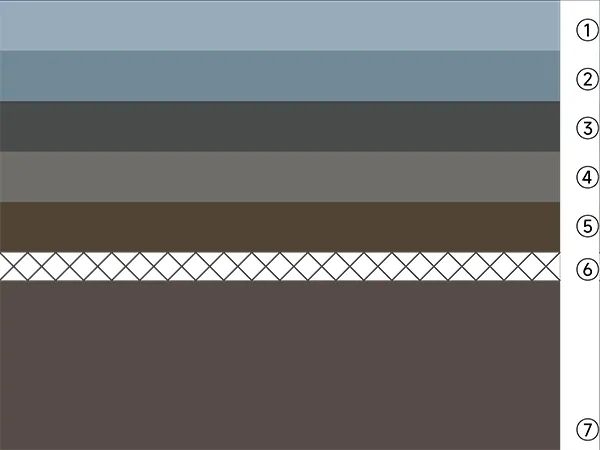
- 1. Topcoat
- 2. 0.8-1mm intermediate coat
- 3. 0.3mm intermediate adsorption layer (to prevent acid liquid and acid gas from penetrating)
- 4. 0.8-1mm intermediate coat
- 5. 0.2mm primer
- 6. Steel mesh
- 7. Metal panel
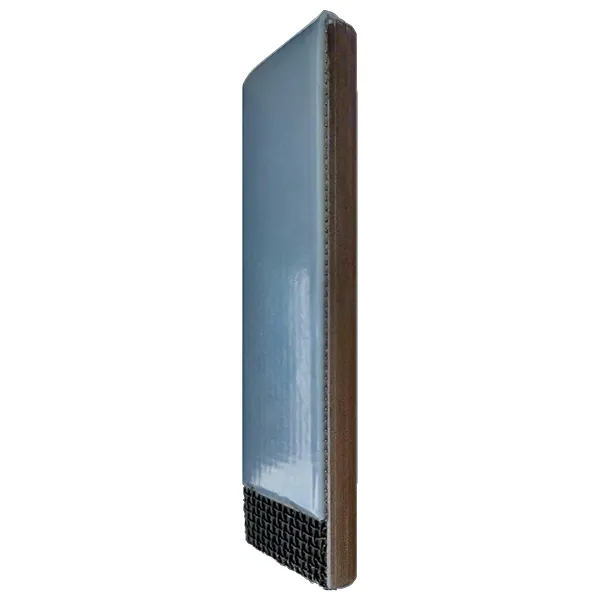
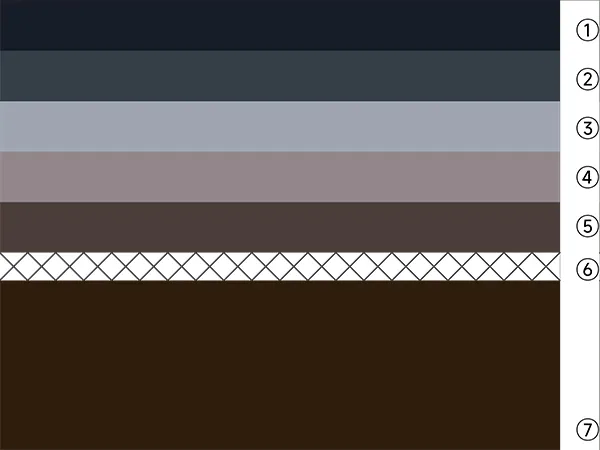
- 1. Topcoat
- 2. 0.8-1mm intermediate coat
- 3. 0.3mm intermediate adsorption layer (to prevent acid liquid and acid gas from penetrating)
- 4. 0.8-1mm intermediate coat
- 5. 0.2mm primer
- 6. Steel mesh
- 7. Metal panel
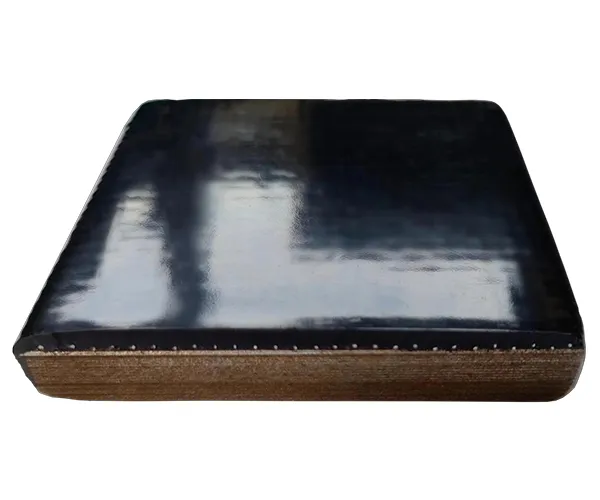
Steel mesh-reinforced sintered fluoropolymer
coating thickness: 1.8 mm ± 0.2 mm
- Advantages
Stable under extreme vacuum at 240°C, with up to 20 years of service life; excellent resistance to halogens, alkalis, abrasion, and impact. Ideal for harsh, demanding conditions. - Disadvantages
Higher processing cost, longer production cycle, and poor heat transfer with jacketed heating.
Standard sintered fluoropolymer
coating thickness:0.8–1 mm
- Advantages
Short processing cycle, low cost of applying corrosion protection coatings, thermal conductivity reaches 80%–85% of enamel, and suitable for parts with irregular shapes. - Disadvantages
Short service life, poor resistance to mechanical damage, and unstable performance when exposed to halogens and organic solvents.
Standard fluoropolymer
lining thickness:2–4 mm
- Advantages
Low cost of applying corrosion protection linings; suitable for on-site application on large equipment with no limitations on length or diameter; offers broad chemical resistance and long service life; excellent wear and impact resistance; seamless application without segmentation. - Disadvantages
Limited temperature tolerance, poor vacuum resistance, inefficient heat transfer with jacketed systems, and unsuitable for highly irregular equipment.
ETFE (F40) rotational lining (single-forming process)
thickness: 2–3 mm
- Advantages
Uniform heating allows one-time melt processing with no seams or joints. - Disadvantages
Moderate corrosion resistance, poor vacuum tolerance, inefficient jacketed heat transfer, not suitable for complex shapes, high cost, and long processing time.
F4 rotational lining with mesh (single-forming process)
thickness: 3.5 –5.5 mm
- Advantages
Uniform heating and single melt-forming process, resulting in a seamless structure. - Disadvantages
Not resistant to negative pressure above 100°C; poor heat transfer in jacketed equipment; not suitable for parts with complex shapes; high cost of applying corrosion protection coatings/lining; long processing time.
PTFE sheet-wrapped
lining - thickness: 3–5 mm
- Advantages
Low cost of applying corrosion protection linings, short processing cycle, excellent wear and impact resistance. - Disadvantages
Flanged connections required for top and bottom heads, straight sections limited to 3m, poor vacuum and temperature resistance, prone to delamination, low thermal conductivity, not suitable for irregular structures.
Based on actual industrial equipment operating conditions, we offer two sintered coating thickness options for ultra-pure powder fluoropolymer applications. The standard type features a general thickness range, while the enhanced type provides additional durability and corrosion protection.
Both options are suitable for high vacuum environments (up to -0.1 MPa) and can withstand temperatures from -190°C to 260°C.
Standard Mesh-Reinforced Coating | Enhanced Mesh-Reinforced Coating | |||
Thickness range | 0.8mm~1.2mm | Thickness range | 1.8mm~2.2mm | |
Application | Suitable for general chemical equipment where reducing cost is a concern | Application | Ideal for more aggressive conditions,such as shorter equipment lifespan or acidic applications (e.g.,plating tanks,G20 alloy,hydrochloric acid,etc.) |
Physical Property Comparison of New vs Traditional Sintering Process
New Process | Traditional Process | |
Corrosion and Permeation Resistance Comparison Analysis using an Atlas Cell corrosion testing device Test conditions:20% hydrochloric acid (HCl),220°C,duration:668 hours | ![]() | ![]() |
Surface Molecular Distribution Comparison Microscopic magnification of ultra-pure fluoropolymer vs other brands | ![]() | ![]() |
Traditional linings rely on adhesive bonding, which limits temperature resistance to around 150°C. Excessive heat can cause adhesives to combust or degrade, posing both safety and environmental risks. In contrast, our laser-welded rivet process enables high-temperature resistance up to 260°C without introducing pollutants. This cleaner, more sustainable method can also be performed on-site, making it ideal for large-scale equipment such as ship compartments and strong acid storage tanks. The flexibility of this solution makes it suitable for demanding and large-format applications.